What Does Premier Aluminum Llc Do?
Getting The Premier Aluminum Llc To Work
Table of ContentsExamine This Report on Premier Aluminum LlcSome Of Premier Aluminum LlcThe smart Trick of Premier Aluminum Llc That Nobody is Discussing3 Simple Techniques For Premier Aluminum Llc
(https://peatix.com/user/25999887)Using reduced cost and unqualified distributors can trigger quality problems, and squandered time and money in the lengthy run. To help you via the procedure, below are some points to take into consideration when choosing the best metal casting provider.
A company that just utilizes the investment casting procedure will attempt to offer you on why that process is best for your application (Aluminum Casting). What if making use of the sand casting procedure is best for you and your requirements? Rather, try to find a provider that uses a variety of casting processes so the finest option for YOU is chosen
If collaborating with a solitary source for every one of your spreading needs is very important to you, the supplier needs to be diverse in its capacities. When incorporated with other integrated abilities, this can aid streamline and compress the supply base. When choosing the appropriate casting provider, mindful consideration must be provided to quality, solution, and price.
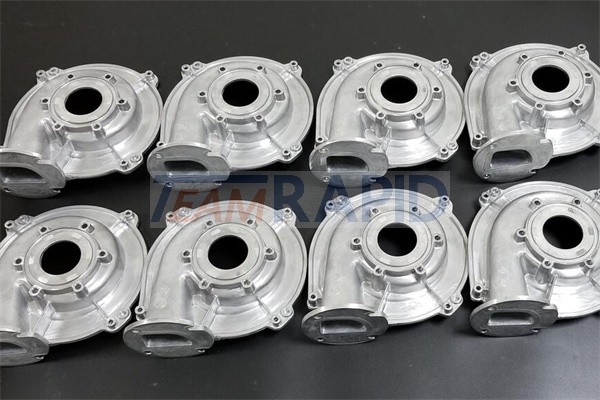
Examine This Report on Premier Aluminum Llc
Buyers progressively pick spreading suppliers who have machining abilities. This can stay clear of problem if issues are uncovered throughout machining. If a 3rd party is machining, it may lead to "finger-pointing" regarding who is at fault. Is it a spreading issue or a machining issue? If the spreading provider uncovers an issue during machining, the trouble is solved faster without disagreement over whose mistake it is.
Problem or no, incorporated machining simplifies the supply chain and decreases dealing with time and shipping price prior to the product makes it to the customer. What do you require from your casting supplier? Are you looking for a person to just supply a metal part to your doorstep or do you require much more? If you do not have internal metallurgy know-how, confirm that the supplier can provide support in selecting the appropriate alloy based on your details application.
Others will go beyond the letter of the PO to aid you save money and time. Do you have demands for both useful link ferrous and non-ferrous alloys? Some factories are minimal or specialized. See to it the provider can fulfill all your material or alloy demands to eliminate the requirement for multiple providers.
Some Of Premier Aluminum Llc

Research the provider's web site. Talk to a sales representative or company partner.
Aluminum is also lightweight and has good rust resistance, making it ideal for applications where weight and sturdiness are necessary factors. Furthermore, aluminum spreading is an affordable approach of production, as it calls for less energy and sources than other techniques. Iron casting, on the various other hand, involves putting liquified iron into a mold and mildew to develop a wanted shape.
About Premier Aluminum Llc
Iron spreading is likewise able to stand up to high temperatures, making it suitable for usage in applications such as engine parts and commercial equipment. Iron spreading can be much more costly than light weight aluminum spreading due to the higher cost of raw materials and the energy needed to thaw the iron. When determining between aluminum casting and iron casting, it is crucial to consider the specific requirements of the application.
If strength and longevity are much more crucial, iron spreading might be the better alternative. Other elements to consider include expense, manufacturing volume, and lead time. To conclude, both aluminum spreading and iron spreading have their very own one-of-a-kind advantages and negative aspects. By very carefully considering the particular demands of the application, producers can choose the very best process for their product.ZheJiang Dongrun Casting Sector Co,. Ltd was integrated in 1995, We have remained in the casting sector for even more than 25 years. Die casting is the name provided to the
process of creating intricate steel components with usage of mold and mildews of the component, also called passes away. The process utilizes non-ferrous steels which do not include iron, such as aluminum, zinc and magnesium, because of the preferable homes of the steels such as reduced weight, higher conductivity, non-magnetic conductivity and resistance to corrosion. Pass away spreading manufacturing is quick, making high production levels of components easy.
It generates even more parts than any type of various other procedure, with a high level of accuracy and repeatability. To find out more concerning die casting and die casting materials used at the same time, continued reading. There are three sub-processes that drop under the classification of die casting: gravity die casting (or irreversible mold and mildew spreading), low-pressure die casting and high-pressure die spreading. The pure metal, also called ingot, is included to the furnace and maintained the molten temperature level of the steel, which is then movedto the shot chamber and infused into the die. The pressure is then maintained as the steel solidifies. Once the steel solidifies, the cooling process starts. The thicker the wall of the part, the longer the cooling time as a result of the amount of indoor metalthat also requires to cool. After the element is totally cooled down, the die cuts in half open and an ejection mechanism pushes the element out. Complying with the ejection, the die is shut for the following injection cycle. The flash is the extra product that is cast during the procedure. This must be trimmed off using a trim tool to
leave just the primary part. Deburring gets rid of the smaller sized pieces, called burrs, after the trimming process. Lastly, the part is polished, or burnished, to offer it a smooth coating. Nevertheless, this confirmed to be an imprecise examination, because the tester might reduce right into an item and miss out on a location with porosity. Today, leading makers use x-ray testing to see the entire interior of parts without reducing right into them. This allows them to much more properly accept or reject components. To reach the completed product, there are three primary alloys utilized as die casting material to select from: zinc, aluminum and magnesium. Zinc is one of one of the most used alloys for die casting because of its reduced expense of raw materials.